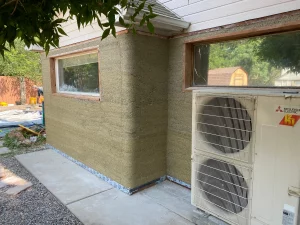
(Photo courtesy of Rocky Mountain Hemp Build)
This story has been corrected to update the number of U.S. homes built with hempcrete.
Cement is cheap, easy to work with and has been the standard of modern construction for decades.
But the global cement industry also accounts for 8% of carbon emissions.
In an effort to mitigate its carbon footprint, various cement and concrete producers around the globe recently announced a roadmap to achieve net-zero concrete emissions by 2050, and cut emissions by a quarter by 2030.
One way to get there is hemp concrete, or hempcrete, which sequesters carbon rather than releasing it, according to Tommy Gibbons, the co-founder and COO of Hempitecture.
His Ketchum, Idaho-based company makes hemp insulation and was awarded a grant by the Department of Energy’s Innovative Crossroads program for research and development of hemp insulation.
Hempcrete is made by wet-mixing hemp hurd with lime. The mixture becomes a moldable substance that’s shaped into a block, creating a lightweight material used for walls and insulation.
“A lot of plant-based materials can do the same thing that other materials can do, and do so in a much more sustainable and carbon-negative way,” Gibbons said.
Despite its ability to fight off pests, mold and even fire due to its thermal mass, like the nascent hemp industry as a whole, hemp construction is still a niche market waiting to break through into the mainstream. It’s got a long way to go, explains Roland Gyallay-Pap, one of the founders of the Boulder-based Rocky Mountain Hemp Build.
“There’s a big drive now in all industries to become more sustainable,” Gyallay-Pap said.
“The construction industry has its own target to become carbon (neutral) by 2030, and there’s a huge interest in alternative building methods. The problem is that in some parts of the U.S. there’s a stigma against hemp itself, which takes time to get over.”
There’s another problem. The United States legalized hemp production just three years ago, after passing the 2018 Farm Bill.
Aside from lingering stigma, and limited education about the plant, hemp cultivation in the United States since legalization has focused on producing it to extract CBD and other non-intoxicating cannabinoids. While the CBD industry experiences a glut, hemp’s undeveloped industrial supply chain has been stuck inside a niche market.
Still, interest in cultivating hemp for use other than CBD and other cannabinoids is growing.
Manufacturing hemp for building and construction materials has seen dramatic interest and escalation in places like Canada and Europe, and some believe the United States will see a similar trend.
“European countries are doing similar things for newer buildings, and the U.S. government seems to have taken an interest in that too,” Gibbons said.
“There are signs that this could be where the industry is going as a whole.”
Baby steps
Compared to the United States, where there are roughly 200 homes made of hemp, in France there about about 2 million, according to Gyallay-Pap.
The idea of using hemp as an alternative method for construction was born out of France in the 1980s.
“The country was looking for materials to use to renovate centuries-old buildings that had been previously renovated with Portland cement,” says Roland Gyallay-Pap.
The French government found hemp to be the most viable due to the fact that it lets moisture pass through, without the risk of mold or pests.
France never outlawed hemp production, adds Gyallay-Pap. As the industry advanced and countries like Canada and others in Europe decriminalized hemp years ago they’ve been leading the market on hemp construction, too.
Last year Netherlands-based hemp manufacturer and Europe’s largest independent hemp grower, HempFlax, acquired the German natural fiber insulation producer, Thermo Natur GmbH & Co.
Last August, the Canadian firm Global Hemp Group went under contract to purchase over 800 acres of land in Hayden, Colorado, initiating its HAIZ project, which aims to develop affordable housing made of hemp materials during the next two decades.
Keeping up with growing demand
Hemp has faced some challenges breaking into existing and established markets.
But its potential is peeking through, and both Gyallay-Pap and his business partner, Eamonn McNaughton, the co-founder of Rocky Mountain Hemp Build, have experienced a surge of interested clients looking to incorporate hemp into their homes and buildings.
Located in the country’s longest hemp-producing state, McNaughton and Gyallay-Pap work with several hemp farmers in Colorado, but access to lime is tricky due to the ongoing supply chain disruption caused by the pandemic.
“Hemp is a big part of the material, but the lime is the other huge piece,” McNaughton said.
Because of the expense to ship limestone from overseas, he and Gyallay-Pap found it a lucrative business strategy to incorporate a small amount of conventional Portland cement in their hempcrete recipe.
While sustainability sticklers may scoff at that idea, the duo says the carbon footprint of shipping more limestone from overseas far outweighs the inclusion of a small amount of conventionally produced cement.
As a budding sector in both the hemp and construction industries, establishing best practices and weighing options for sustainability is crucial for long-term growth, according to Gyallay-Pap and McNaughton.
“The world of concrete is a big, big world,” Gyallay-Pap said. “We’ll be the small ax chopping down the big tree.”
“We’re seeing a lot of projects coming up in the spring and summer, to the point where getting material might even be a bit of an issue.”
Hilal Bahcetepe can be reached at [email protected].