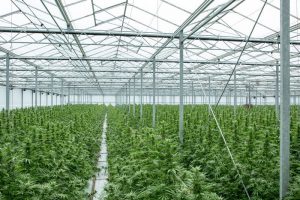
Cannabis producers looking to sidestep the wild fluctuations of climate change and extreme weather events by growing their crops in a protected greenhouse environment may recognize that there is great deal of consideration, planning and capital that goes into greenhouse construction.
But there’s no such thing as being too prepared when it comes to designing and building out a cannabis greenhouse facility.
Once up and running, a profitable cannabis greenhouse facility successfully balances operational costs with a high-quality, uniform harvest.
It’s common to undermine success from the start of the project if detail isn’t top of mind through each step, from design to build-out, and selecting operational components such as benching systems and environmental controls.
Greenhouse cannabis producers should start with their business goals and think backward. What do they want their brand to represent in the marketplace?
“It comes down to understanding your craft and what you’re going for. Knowing what you want will increase or decrease what you’re going to spend on that greenhouse,” said Hamilton Nelson, a veteran cannabis producer who is currently sales and operation manager at Square One Starts, a hemp young-plants provider in Aurora, Oregon.
At an estimated $35 to $50 per square foot in upfront costs, greenhouse cannabis producers can save significant money by spending the time on a well thought-out and executed plan.
The last thing a grower wants to do is retrofit their greenhouse after they built it because it doesn’t work well for growing cannabis.
Choosing a greenhouse structure and location
Producers should start by asking what they want in a greenhouse, said Derek Smith, executive director of the Resource Innovation Institute, a non-profit organization working to promote efficiency in resource-intensive agricultural sectors like cannabis.
Greenhouses can be built from many different materials. For example, polyethylene-covered hoop houses with roll-up sides are relatively inexpensive and straightforward compared to large glass or polycarbonate facilities using sophisticated environmental controls.
“In other words, how much of a controlled environment is it? There’s a huge difference between a hoop house and a state-of-the-art, fully sealed, highly automated greenhouse that is, to some degree, operating like an indoor environment but with sunlight,” Smith said.
Next, think about where the greenhouse is located.
Climate and light levels can significantly influence construction materials and other greenhouse components. For instance, location can impact your heating and cooling systems and lighting needs, and ultimately determine fundamental requirements such as electricity, Smith said.
Understanding total infrastructure needs can also help drive efficiency.
“You’ve got to understand what your power needs are and then determine the right mix of energy that you can bring to the site,” Smith said.
“You may need propane, natural gas or delivered fuels. You could set up a micro-grid and do on-site renewables in tandem with natural gas …but it all starts from knowing how much power you’re going to need.”
Another crucial consideration is the water table and soil composition at the construction site, Nelson said. Install drainage before building if a site is located on top of a high water table or downhill from areas of significant run-off.
The permitting process
Growers also need to think about the planning and permitting process, said Johnny Burgoon, solutions architect for the cannabis greenhouse division of Prospiant, a Cincinnati-based controlled-environment greenhouse solutions provider.
Many states have time limits on their licenses, requiring growers to be in operation or at least show significant process, Burgoon said. West Virginia has a six-month requirement.
“We’ve had people lose their license because they didn’t get up and running fast enough,” Burgoon said.
Zoning is another complication most greenhouse operators don’t consider beforehand, Burgoon said. Local approval will depend on land-use regulations, which typically include buffering requirements or proximity to other public facilities, like a church or a school. The population density of an area can also restrict zoning for a greenhouse facility.
Other local land-use regulations might include odor management, noise requirements, impact on traffic, signage and even the facility’s appearance, Burgoon said. This is above and beyond typical state licensing requirements for marijuana growers for requirements such as security.
“Before you even get into the actual building permits and codes, zoning is the most important thing because that will let you know if you can even have it there or not,” Burgoon said.
Marijuana growers need to understand that since marijuana production is governed under per-state manufacturing rules, not a federal agricultural rule like hemp, their greenhouse will be required to meet standard building codes. Not all greenhouse designs meet building requirements for things like snow load, wind or fire suppression, Burgoon said. However, hemp greenhouse facilities are typically exempt from needing building permits, providing more flexibility for hemp greenhouse facilities.
Ideally, growers consult with him before they start anything else, Burgoon said.
“Quite often, we get people that come through who don’t have all three necessities — they’ve got a license, but they don’t have a property and they don’t have funding,” Burgoon said.
“It’s really smart on their part if they engage a design-build before they even have all three.”
Check out the newest MJBizDaily Buyers Guide: Greenhouse Components to learn about how to minimize project delays, hire experienced builders, select greenhouse systems and plan for scale and efficiency by building the proper infrastructure in a greenhouse site, along with guidance on selecting greenhouse automation, irrigation and benching systems.