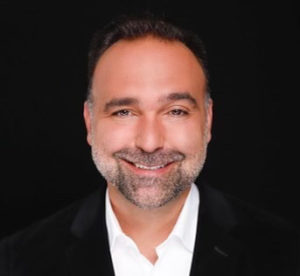
Aitor Arrieta
Editor’s note: This story is part of a recurring series of commentaries from professionals connected to the hemp industry. Aitor Arrieta is vice president of GenCanna, a CBD manufacturer in Kentucky.
Supply chains are key to any company’s success, but they’re especially important in the CBD industry.
Brands need to find suppliers that can deliver a reliable and accessible product and that have sufficient manufacturing and processing capacities to meet escalating demands.
As the industry continues to grow, distributors and consumer-facing retailers need to do their homework when evaluating and choosing the right supplier, which could make the difference between long-term success and calamity.
Demand for CBD products is growing rapidly. The U.S. market for CBD will reach $6.9 billion in sales by 2025, according to Nielsen and Hemp Industry Daily projections.
With this increase in market demand, brands need to be strategic as they select suppliers.
There are many instances where manufacturers have miscalculated or misstated their production capacities, which has had cataclysmic effects on distribution and retailers who are then left scrambling to find quality product alternatives at acceptable costs.
Single source
Conducting due diligence on the manufacturer’s capabilities should be an essential part of any CBD distribution and retail process.
Rather than rely on a broker who subcontracts manufacturing and processing operations, a buyer should collaborate with a single provider that can deliver all the capabilities necessary for producing consistent, reliable and compliant goods to market on time and on budget.
Having that “one throat to choke” will save distributors time, money and stress. That is completely opposite from the experience many CBD brands, have dealing with brokers who have little control over outsourced processes.
When choosing product suppliers, distributors and retailers need to consider several aspects for meeting demand while also adhering to quality mandates. Specifically, supply capacity, consistent quality and certifications are all components of a reliable supply chain and are necessary for making regulatory- compliant CBD products that satisfy consumer expectations.
Supply capacity
All distributors recognize that consumer interest fluctuates for CBD products, and the ability to keep products on store shelves and in ecommerce carts can be especially challenging when demand spikes. Experienced suppliers that have ample capacity can seamlessly manage changing demand in a timely manner. While some suppliers say they have excess capacity, they could very well be relying on independent, unaudited and uncontrolled broker relationships that outsource manufacturing to a third party.
When control is ceded, quality can certainly wane, and schedules can come off the rails based on external factors like scheduling, staffing, weather, access to biomass and transportation.
Choosing a partner with sufficient manufacturing capacity, access to raw materials, integrity and in-house experience is critical for success.
It’s important to ask hard questions, especially about outsourcing, to tour the manufacturing facilities, and to require guarantees that the manufacturer will deliver a consistent product on time and on budget.
Consistent quality
Many suppliers buy raw material like biomass on the open market. But unless that biomass is from a single, traceable source, there’s a good chance the final CBD product will not have a consistent look, feel and chemical makeup.
Every grower’s hemp varies in quality, and when manufacturers use CBD and other bulk cannabinoid ingredients from a variety of sources, creating a consistent, high-quality product is difficult.
In the finished-goods world, this is especially important. When customers repeatedly purchase the same product, they expect that the quality is consistent.
Experienced manufacturers should have a reliable and consistent biomass source, which is the foundation for delivering a quality product that adheres to brand specifications and consumer expectations.
Distributors should ask suppliers about the raw material they use, including:
- Where it’s grown.
- Available quantities.
- What actions are used in case of a shortfall in supply.
The suppliers should also ensure the third-party lab used for testing is fully accredited.
Consider that retail chains often require that products have Global Food Safety Initiative (GFSI) accreditations like BRCGS or SQF, which mandate a recall system in place to remove unsafe product from the market before it reaches the consumer.
Suppliers should use a reputable third-party lab that is accredited by a recognized accreditation body that audits the laboratory against a known standard, the most common of which is ISO17025. But it isn’t enough to choose a lab that has a blanket accreditation. Suppliers should verify that the tests needed to ensure product quality and consistency are included in the scope of the laboratory’s accreditation, otherwise the entire process is disingenuous.
Certifications
Maintaining the appropriate certifications is probably the most complicated task for suppliers to ensure products are in compliance.
But beware of shortcuts.
There are numerous regulatory bodies and organizations that certify hemp-based products. Any product that is not properly certified — be it in processing, labeling or some other key factor —could be pulled from shelves or fail to pass internal standards.
The repercussions can be disastrous for retailers, distributors, consumers, the brand itself, and denigrate the industry. Distributors and retailers need to work with manufacturers that can demonstrate a supply chain that is reliable, compliant, and traceable.
How important are certifications? Consider that retail chains often require that products have Brand Reputation through Compliance certifications, which mandate a recall system in place to remove unsafe product from the market before it reaches the consumer.
As part of this certification, manufacturers are required to do a minimum of three mock recalls a year, but more experienced manufacturers may complete as many as six mock recalls in this time-frame. There are various other certifications for state and local government usage, religious practices and other instances, which add to the complexity of managing these requirements.
The chain of custody is important for all finished goods, and buyers need to verify the source of the biomass. Documenting this process is important, so retailers should ask manufacturers to produce detailed reports that explain how a product evolves from raw material to a finished good.
Relying on a partner that is properly certified can also insulate the channel and retailer when a problem does arise.
Experienced manufacturers should be able to provide an affirmations document that details all the certifications related to supply chain and manufacturing processes. This should stipulate that any outside vendors the manufacturer uses are also similarly vetted.
Conclusion
As demand for hemp-based products continues to increase, there is more pressure on distributors and retailers to place quality, reliable products on shelves and online.
While some manufacturers may make claims regarding their production capabilities, this is an industry with no margin for error.
Providers need to ask manufacturing partners how they manage capacity, ensure quality and oversee compliance. Using a supplier with modern, efficient and compliant production facilities, access to raw material and certification expertise can accelerate growth, create a reputation for excellence, and avoid what happens all too often: product failure, lost customers and lost gross-margin dollars.
Arrieta can be reached at [email protected]